The Control System intended for optimal control of the furnace burning process, air-gas ratio, heat recuperation, waste gases utilization in the process of iron-ore sintering by the conveyor-type machine OK-306.
OJSC «Nothern Mining», Kryvy Rig
The Control System intended for optimal
control of the furnace burning process, air-gas ratio, heat
recuperation, waste gases utilization in the process of
iron-ore sintering by the conveyor-type machine OK-306.
SW / HW platform
• High-reliability redundant process controller Q-System
(CPU type - Q25PH) from Mitsubishi Electric to
manage a number of plain and cascade PID-loops.
• Distributed controller’s architecture based on a remote
I/O’s and a redundant (dual) optical ring network
MelsecNet/H.
• Developing Software “PX-Developer” with built-in
functions for PID-loop’s auto-tuning procedures (to find
an optimal set-up parameters)
• High level Human-Machine Interface (HMI) based on
the world first class “Citect-SCADA” visualization and
control Software.
Gas fuel specific rate reduction from 19,0
to 15,5..16 q.m./ton due to a heat
recuperation and re-arranging of an air
/gas / waste-gas flows;
• Increasing production output from 235 to
280 ton/hour due to the thicker iron-ore
layer on the conveyor and sophisticated
drying and pre-heating procedures;
• Automatic optimal “air / fuel“ ratio for
multiple furnaces;
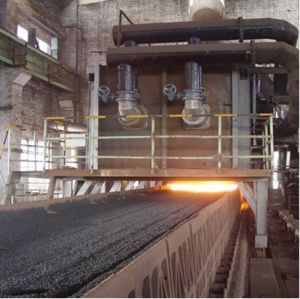